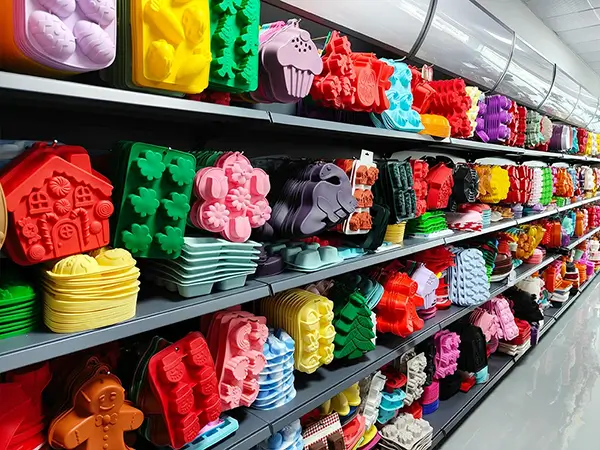
Finding the right manufacturer is not just about price—it's about precision, reliability, communication, and long-term value. In today’s competitive market, businesses need partners who can deliver consistent results, meet deadlines, and provide technical expertise throughout the development process.
Start with Industry Experience and Specialization
The first thing to consider when searching for a custom silicone mold manufacturer is their experience in your specific industry. Silicone molding is used in many sectors, including healthcare, automotive, electronics, food-grade applications, and consumer goods. Each of these industries has unique standards, tolerances, and safety requirements.
A manufacturer who specializes in your field will understand the technical and regulatory expectations of your project. They will also be more familiar with suitable materials, mold designs, and post-production processes. Checking the manufacturer’s portfolio or past projects can give you insight into their expertise and capabilities.
Evaluate the Quality of Equipment and Technology
A reliable manufacturer invests in modern, high-precision equipment. The technology they use directly impacts the accuracy, finish, and performance of the final mold. Look for manufacturers that use CNC machines, automated molding equipment, and advanced CAD/CAM software to design and produce molds.
Ask whether they offer in-house prototyping and testing. The ability to quickly create and modify prototypes is crucial during the early stages of development. It also reduces the risk of production errors and allows you to refine your product design before moving into large-scale manufacturing.
Review Their Customization Capabilities
Not all silicone mold manufacturers offer the same level of customization. Some may only work with standard mold shapes or sizes, while others provide complete flexibility in designing molds from scratch. Make sure the manufacturer is capable of handling the complexity and detail required for your product.
Customization may include specific surface finishes, tight tolerances, multiple cavity molds, or integration with other parts and components. A good manufacturer will collaborate with your design team, offer suggestions, and ensure that the mold is optimized for performance, durability, and production efficiency.
Check for Material Expertise and Selection
Silicone comes in a variety of grades, including medical-grade, food-grade, and industrial-grade formulations. The type of silicone used in your project will affect safety, compliance, and performance. A qualified manufacturer will guide you in selecting the best material based on your application, temperature requirements, chemical exposure, and mechanical stress.
Ensure the manufacturer sources high-quality silicone from trusted suppliers. They should also be able to provide certificates of compliance and documentation for regulatory approvals, such as FDA, RoHS, or ISO standards.
Assess Communication and Technical Support
Clear and consistent communication is essential when working on a custom manufacturing project. You need a partner who responds promptly, understands your technical language, and provides regular updates on project progress.
Pay attention to how well the manufacturer explains their process, answers your questions, and handles revisions. A manufacturer who offers full support—from design consultation to final delivery—is more likely to meet your expectations and timelines.
Technical support should extend beyond the initial mold creation. The best manufacturers provide ongoing service, maintenance recommendations, and troubleshooting in case any issues arise during production or product use.
Verify Certifications and Quality Control Practices
Before finalizing your choice, ask about the manufacturer’s certifications and quality control procedures. A reliable company follows strict inspection and testing protocols to ensure that each mold meets design specifications and functional requirements.
Look for manufacturers certified with ISO 9001, which indicates strong quality management systems. If you're developing products for specialized markets such as medical or aerospace, additional certifications may be necessary.
A good manufacturer also performs regular inspections during mold production and product testing. These checks can include dimensional accuracy, surface finish, cavity alignment, and material consistency. This attention to detail minimizes defects and supports product consistency in large-scale production.
Compare Lead Times and Delivery Reliability
Time is often a critical factor in product development. Delays in mold production can push back your entire timeline and increase costs. When choosing a manufacturer, ask about their typical lead times for design, prototyping, and full-scale mold production.
Also, find out whether they can meet your deadlines and handle urgent projects if needed. A reliable manufacturer should have the capacity and workflow systems to accommodate your schedule without compromising on quality.
Delivery reliability includes more than just the initial shipment—it means being able to count on the manufacturer for future batches, reorders, and revisions. Building a long-term relationship with a dependable supplier ensures smooth production and ongoing product support.
Request Samples or Visit the Facility
Whenever possible, request samples of previous molds or finished silicone products. This will give you a real sense of the manufacturer’s capabilities and the quality of their work. Examine the details, surface finish, and consistency across multiple items.
If you are managing a large or complex project, consider visiting the manufacturer’s facility. A site visit allows you to see their operations firsthand, meet the engineering team, and better understand their production process. It also helps build trust and clear expectations from the start.
Read Client Reviews and Ask for References
Client feedback can offer valuable insight into a manufacturer’s reliability and professionalism. Look for reviews on third-party platforms or industry forums. Ask the manufacturer to provide references from previous clients who had similar project requirements.
Speaking directly with past customers can reveal strengths and weaknesses that may not be obvious during initial conversations. It also helps confirm that the manufacturer has a history of delivering quality results on time and within budget.
Conclusion
Finding a reliable custom silicone mold manufacturer is a crucial step in ensuring the success of your product. The right partner will offer industry-specific knowledge, high-quality materials, advanced equipment, and excellent customer support. They will work with you throughout the entire process—from initial design to final delivery—to create a mold that meets all functional, regulatory, and aesthetic requirements