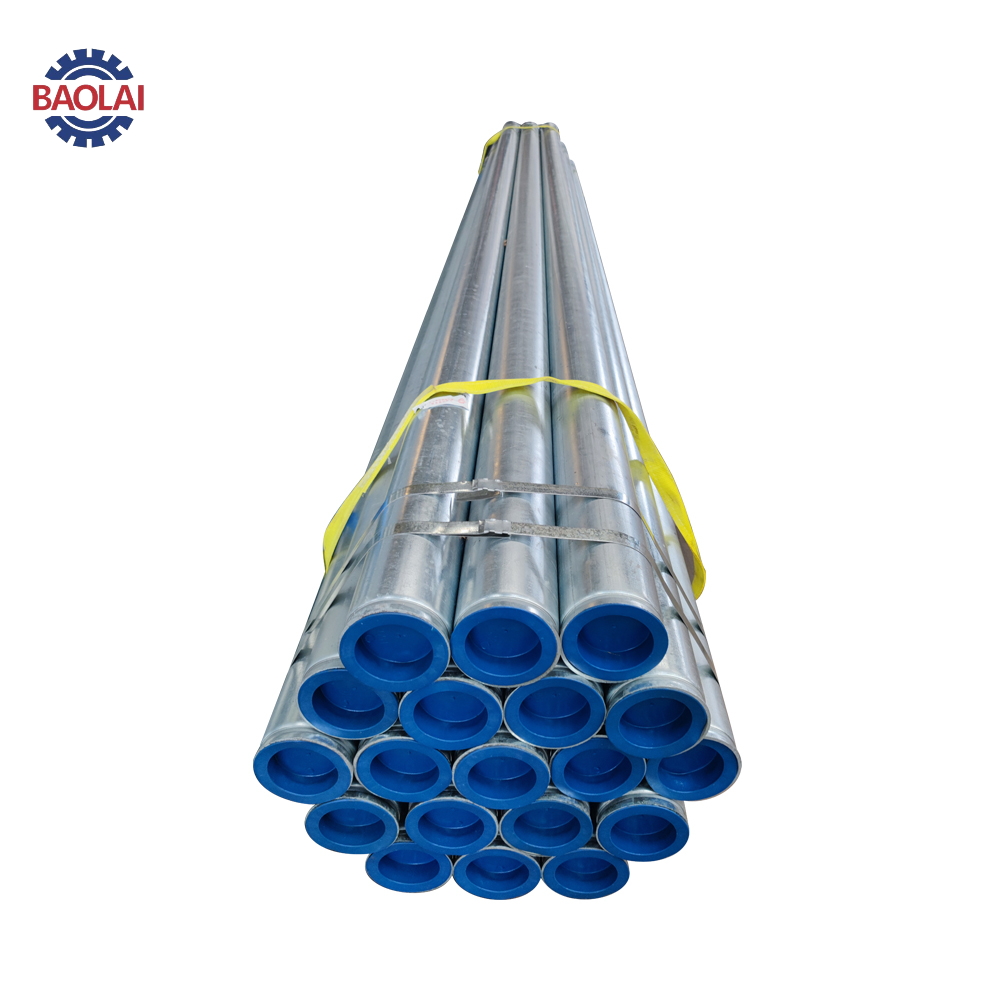
By understanding the different factors that influence ERW pipe performance, you can make informed decisions that improve project efficiency and avoid costly replacements or failures.
Know Your Application Requirements
The first step in selecting the right ERW pipe is identifying the needs of your specific application. Whether the pipe will be used for structural support, fluid transport, mechanical systems, or fencing, the intended use will determine the necessary material strength, diameter, wall thickness, and coating.
For structural applications like columns or trusses, high strength and dimensional stability are key. In fluid transport systems, internal pressure handling and corrosion resistance take priority. Each application brings a unique set of challenges, and understanding them will help you narrow down your choices effectively.
Choose the Correct Pipe Size and Wall Thickness
Pipe size and wall thickness play a crucial role in determining the load-bearing capacity, flow rate, and overall strength of the ERW pipe. In structural uses, thicker walls may be needed to support weight and resist external forces. In piping systems, wall thickness must match the internal pressure of the fluid or gas being transported.
Pipe diameter must also align with system requirements and design specifications. Undersized or oversized pipes can lead to inefficiencies or failures. Carefully reviewing engineering calculations, flow requirements, and load expectations will help determine the ideal size and thickness for your project.
Evaluate the Type and Grade of Steel Used
ERW pipes can be manufactured from various types of steel, including carbon steel, mild steel, and stainless steel. Each material offers different properties related to strength, corrosion resistance, and workability.
Carbon steel ERW pipes are typically used in high-pressure environments and are common in oil and gas, power plants, and heavy construction. Stainless steel ERW pipes are selected for applications involving corrosive environments, such as water systems, marine structures, or food processing plants. Mild steel ERW pipes are more suitable for lighter structural applications like fencing or scaffolding.
Choosing the right material grade ensures that the pipe can withstand environmental and operational stresses throughout its service life.
Consider Environmental and Operating Conditions
The environment where the pipe will be installed significantly affects the choice of ERW pipe. Outdoor settings, marine environments, chemical exposure, and temperature fluctuations all demand specific material and coating choices.
For outdoor or moisture-rich environments, galvanized ERW pipes are a good option due to their protective zinc coating. If the pipe will be exposed to corrosive chemicals, selecting stainless steel or coated pipes becomes essential. In high-temperature settings, materials with heat resistance and thermal stability should be prioritized.
Evaluating site-specific conditions helps avoid premature wear, corrosion, or mechanical failure.
Check for Compliance with Industry Standards
To ensure the safety, reliability, and compatibility of ERW pipes, it is important to choose products that meet recognized standards such as ASTM, API, ASME, or ISO. These standards govern the chemical composition, mechanical properties, dimensional tolerances, and pressure ratings of the pipes.
Using certified ERW pipes helps ensure that your project passes inspections, meets regulatory requirements, and performs reliably under expected conditions. It also reduces the risk of using substandard materials that could compromise the entire system.
Select the Right Surface Finish or Coating
The surface finish or protective coating of an ERW pipe affects its longevity and suitability for certain environments. Uncoated ERW pipes are typically used indoors or in applications with minimal exposure to moisture or chemicals. For outdoor and corrosive environments, coatings such as galvanization, epoxy, or powder coating provide additional protection.
Some ERW pipes come with black finishes, while others are painted or oiled to prevent rust during transportation and storage. Selecting the right surface treatment based on your application ensures that the pipe remains protected and maintains its performance over time.
Review Pressure and Temperature Ratings
In systems where ERW pipes will be exposed to internal pressure or extreme temperatures, it is essential to choose pipes that are rated for the required performance. Pipes not rated for high pressure may fail, causing system breakdowns, leaks, or safety hazards.
Pressure and temperature ratings are often indicated on the pipe specification sheet and must align with your project’s operational parameters. These ratings should be cross-checked with system design documents to ensure full compatibility.
Look for Supplier Reputation and Certification
Not all ERW pipe manufacturers offer the same level of quality and consistency. Working with a reputable supplier ensures that the pipes you receive are tested, certified, and produced according to international standards. Look for suppliers with quality assurance systems in place, such as ISO 9001 certification or third-party testing certifications.
Reputable suppliers also offer better customer support, technical documentation, and customization options. Choosing a trusted source reduces the likelihood of defects, delays, or compliance issues.
Account for Fabrication and Installation Needs
Different projects require pipes that are easy to cut, weld, bend, or thread. Some ERW pipes are easier to fabricate than others, depending on the material and wall thickness. Understanding your project's fabrication requirements will help you select a pipe that matches your tools and methods.
Proper alignment, secure joints, and precise installation all depend on the compatibility of the pipe with the fabrication process. Choosing the right pipe can simplify construction, reduce labor time, and minimize on-site errors.
Conclusion
Selecting the right ERW pipe based on your application needs involves careful evaluation of several critical factors, including pipe size, material type, environmental conditions, pressure ratings, and industry standards. Taking the time to analyze these factors ensures that the pipe you choose will meet performance expectations, last longer, and operate safely in its intended environment.